Overhead Crane Inspections - Workplace Inspection Checklists
Cranes must be tested and subject to examinations and inspections.
There are strict legal requirements concerning the thorough examination of all cranes: Lifting equipment must be thoroughly examined at the prescribed intervals (every 12 month period).
An annual detailed examination should be completed by a specialist and will usually be arranged by the crane hire company, although it is the responsibility of the crane user to ensure that all necessary examinations are carried out to ensure the crane is safe for use, plus have the required reports in order. Records of thorough examinations and tests must be: readily available to enforcing authorities; secure; and capable of being reproduced in written form.
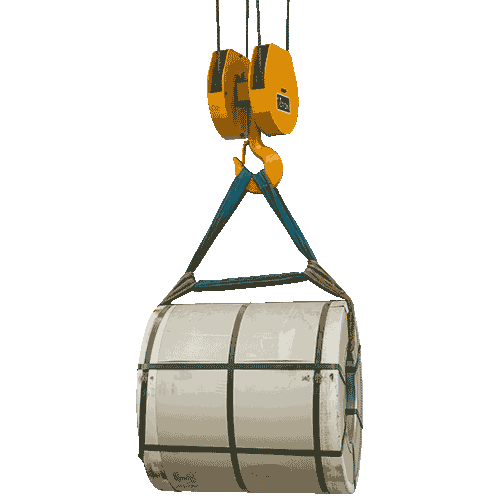
It is important however not to rely solely on this one snapshot in time; companies should also complete regular visual checks throughout the intervening period and that is where the Good to Go Safety system comes into its own. Around a quarter of all crane incidents involve a dropped load, an estimated 60% of which could be attributed to poor crane maintenance and 15% to the failure of wire ropes/cables.
When it comes to the use of overhead cranes (also referred to as an overhead travelling crane or gantry crane) it should be thoroughly examined and tested after erection, substantial alteration or repair and at relevant intervals. Regular safety checks should be carried out and the results recorded. As a general guide, daily pre-use checks should be carried out by the operator, with additional formal inspections carried out at least monthly or in accordance with the manufacturer's instructions where timescales are shorter.
Assuming the risk of deterioration is an ongoing inevitability, the importance of pre-use checks to identify any day-to-day damage or faults cannot be underestimated (especially considering the weight of equipment likely being moved by the crane and the potential damage it could cause should the crane fail in any way - equipment failure can have very serious consequences not just for the load, but also for any plant, building structures or personnel in the surrounding area).
The Good to Go Safety overhead crane inspection checklist system is flexible, allowing pre-shift start, daily, weekly, monthly or annual checks to be implemented – every site is likely to have differing requirements and the Good to Go system can be adopted to suit those needs.
Upon completion of the crane checklist, it is removed from the book and placed inside the tag (we’d recommend to have this secured to the control panel of the crane). The tag will then display the date and findings for that day, ensuring everyone is aware that it has been examined that day. A duplicate copy of the completed checklist is retained inside the book for management records and provides a clear, documented audit trail. If a fault is found then the tag will display a “Do Not Use” message and effectively quarantine the crane until repairs have been carried out and a new inspection deems it safe to use.
Overhead Crane Inspection Books - 25 Checklists
Overhead cranes must be thoroughly examined at least every twelve months to comply with LOLER. It is..
£6.20
Overhead Crane Inspections - Weekly Checklist Kit
Overhead cranes must be thoroughly examined at least every twelve months to comply with LOLER. It is..
£37.10
Overhead Crane Inspections - Daily Checklist Kit
Overhead cranes must be thoroughly examined at least every twelve months to comply with LOLER. It is..
£109.50
Overhead Crane Inspection and Maintenance Station
The information station will provide your workplace with the ideal central location to store inspect..
£233.20
Overhead Crane Poster - Visual Inspection Checklist
Our overhead crane safety poster has been designed to highlight key components of overhead crane and..
£21.77
Inspection Wallet and Pen
A handy wallet that not only provides additional protection from the elements but also gives inspect..
£6.20
Weather Resistant Inspection Holder
These industrial strength pockets have a press seal fastening to keep important documents clean and ..
£6.31
Inspection Book Dispenser
Allow the storage of checklists in a central location for quick and easy access to important inspect..
£13.25